Fixtures, Jigs y Gauges Impresos en 3D, ¿Sirven?
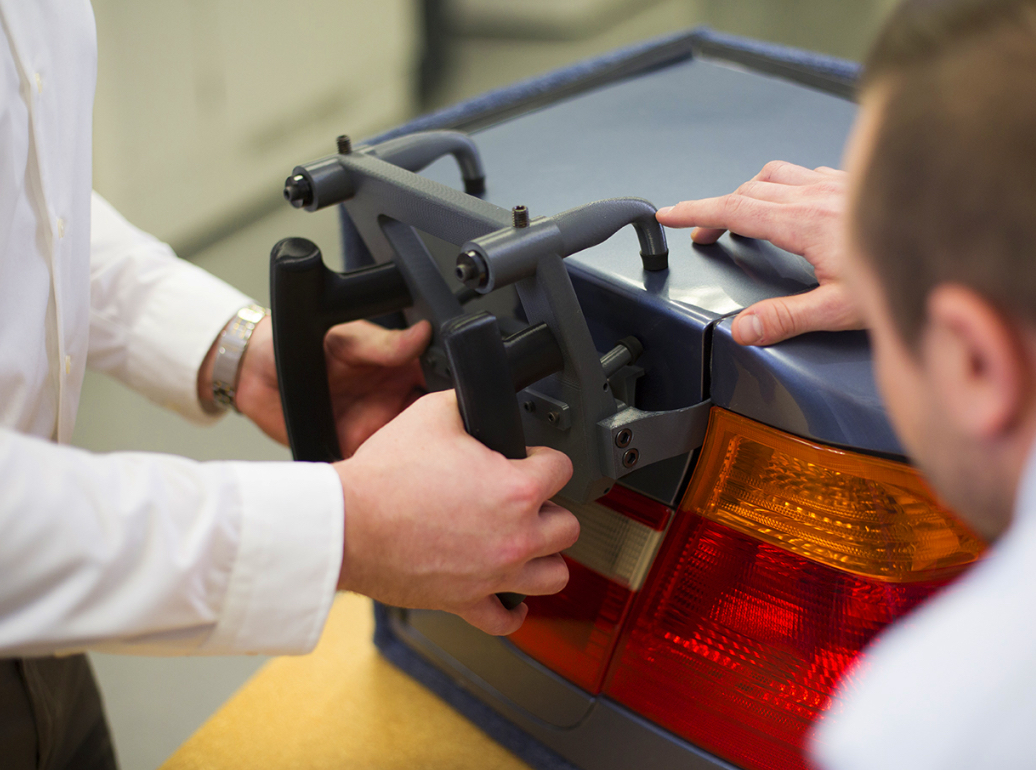
La respuesta es si, para producir algunos Fixture y Jig Tool que soporten el desgaste y exigencia del uso rudo que demandan en un piso de producción, la Manufactura Aditiva es una gran herramienta.
*Ejemplo de aplicación al final del artículo
¿Qué son Fixture y Jig Tool?
Como principio básico de Lean Manufacturing, es necesario poder estandarizar procesos y por ello es tan crucial el uso de Fixture y Jig Tool en nuestras líneas de manufactura para generar repetibilidad.
Los Fixtures y Jigs Tools son herramientas que nos permiten soportar, mantener fijo y localizar una pieza durante su proceso de manufactura o maquinado. La mayor diferencia entre uno y otro, es que un Jig Tool también sirve de guía para la herramienta de operación tal como taladros o colocadores de componentes.
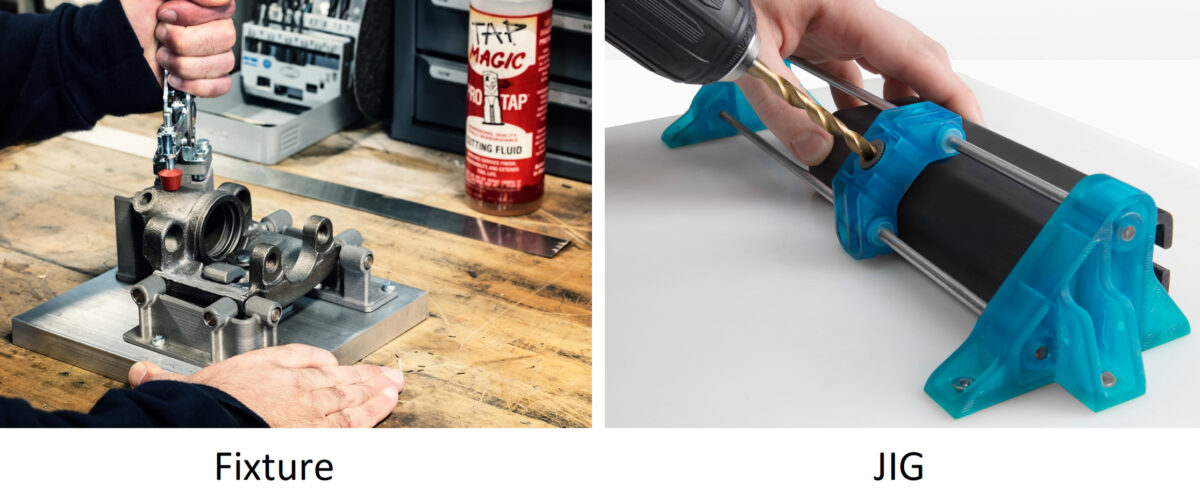
Principalmente son usadas para mantener piezas en posición, guiar un taladro, aplicar soldadura, ensamblar componentes electrónicos, mantener una pieza de forma compleja simple en un maquinado o post proceso CNC.
Sin embargo producir estas herramientas puede tener grandes implicaciones en desarrollo de producto, costo y tiempo de fabricación, que impacta en los lead times de nuestros procesos.
Fabricar en 3D o con Manufactura Aditiva Fixture y Jig Tool
La manera tradicional de hacerlos es mediante maquinados CNC, router y en ocasiones algo artesanal. La tendencia más actual es comenzar a fabricarlos en impresión 3D.
Los tiempos de entrega de un Jig Tool o Fixture tradicionales puede ir de 1 a incluso más de 10 semanas. Los costos varían dependiendo el tamaño, el material y la forma o complejidad de la herramienta; todos estos factores ya no serán un dolor de cabeza con Manufactura Aditiva.
Sin duda, la tecnología de impresión 3D ayuda a fabricar Fixture y Jig Tool confiables, de gran tamaño, resistencia, precisión y sobre todo funcionalidad y flexibilidad a los diseños.
A continuación, te comparto los puntos a considerar sobre la manufactura de Jig Tool y Fixture impresos en 3D.
Tamaño:
Con impresión 3D tienes la capacidad de crear jix y fixtures de una sóla pieza de hasta 90x60x90 cm en materiales plásticos y de hasta 35x30x35 cm en metales.
Piezas de mayor tamaño, pueden fabricarse por segmentos y unirse posteriormente.
Materiales:
La variedad de materiales de impresión 3D es muy grande, pero se divide en termoplásticos y metales. Los termoplásticos más comunes son el ABSM30, PC, ABS-ESD7, Nylon 12 y Ultem, materiales que superan o igualan las propiedades de los plásticos tradicionales usados en estas aplicaciones, como el Nylon, Teflon y Nylamid.
En metales, las opciones son estándares en Aluminio, Acero y Acero Inoxidable.
Resistencia:
Las propiedades de los materiales con los que fabricamos permiten construir herramientas de alta resistencia mecánica que podrán soportar el uso rudo de un piso de producción.
Siempre y cuando el grosor mínimo de la pieza o componente sea mayor a 3 mm, la pieza soportará cualquier tipo de uso natural de una pieza de este tipo, incluyendo caidas, torción y fuerza.
Desgaste:
Quizá una de los mayores dudas sobre la impresión 3D en esta aplicación. Sin duda, piezas impresas en metal tendrán una alta resistencia al desgaste por uso, pero dependiendo de la aplicación, podremos utilizar materiales que resisten el alto desgaste contra piezas metálicas como el PC, Ultem o Nylon 12 reforzado con fibra de carbono.
Hemos hecho piezas que llevan más de 5 años instaladas en pisos de producción y siguen funcionando perfectamente.
Precisión:
Es cierto que la impresión 3D no tiene una precisión de detalle como un maquinado CNC (precisión de +/- 0.01 mm por corte).
En promedio, una pieza impresa en 3D tiene una precisión dimensional total (volumétrica) de +/- 0.2%. Esto quiere decir que si la pieza en total mide 100 cm, podrá medir en su volumen total 100 +/- 0.2 cm, pero en sus dimensiones internas, se respeta la misma proporción. Si una perforación en el modelo 3D mide 20 mm, podrá medir 20 +/- 0.04 mm.
Cuando la precisión debe ser mejor que esto, lo que se puede hacer es rectificar la pieza en un maquinado CNC en los puntos específicos y rectificar las dimensiones para cumplir con las especificaciones del diseño.
Peso:
Sin duda, una herramienta impresa en 3D siempre será más ligera que cualquier pieza fabricada bajo métodos tradicionales (CNC) ya que en su interior, la pieza puede estar ahuecada (con estructuras de refuerzo) y ahorrar material.
Esto sin duda es un plus para el tema de ergonomía y simplicidad de las herramientas.
Forma:
En impresión 3D, la forma siempre será libre. No hay restricciones en geometría. La pieza a fabricar puede tener cualquier geometría sin importar su complejidad.
Componentes adicionales:
A las piezas impresas en 3D se les pueden agregar componentes tales como clamps, sensores, fijadores, pines, insertos metálicos, bujes o cualquier componente externo.
En ocasiones, partes críticas o de mayor desgaste se fabrican mediante metales o CNC y se insertan o incrustan en la parte plástica. Esto permite mucha libertad en el diseño de las herramientas.
Precio y tiempo:
Sin duda, el factor más importante. En promedio, herramientas de este estilo fabricadas con Manufactura Aditiva representan ahorros en costo de hasta un 50% vs métodos tradicionales y metales.
En tiempo, pueden estar listos en menos de 24 horas (dependiendo del tamaño). Una pieza de 60x30x60 cm, queda listo en menos de 4 días.
Caso de aplicación
Para simplificar todo lo que hemos platicado, te compartimos un ejemplo.
Uno de nuestros clientes, fabrica cubiertas plásticas para el interior de las puertas de una camioneta de lujo. Esta camioneta lleva en la parte de la bocina un logotipo de la marca BOSE colocado en una posición estándar y fija.
Originalmente, nuestro cliente utilizaba una plantilla de madera, hecha a mano, que permitía a los operadores colocar el logotipo en posición, sin embargo, la plantilla se dañaba con facilidad.
Se hizo un intento de fabricar la pieza en metal, pero por la geometría de la pieza resultó costoso, sin mencionar que la herramienta era demasiado pesada para quitar y poner más de 100 veces por día.
La solución, una herramienta fabricada en 3D en material Policarbonato (PC).
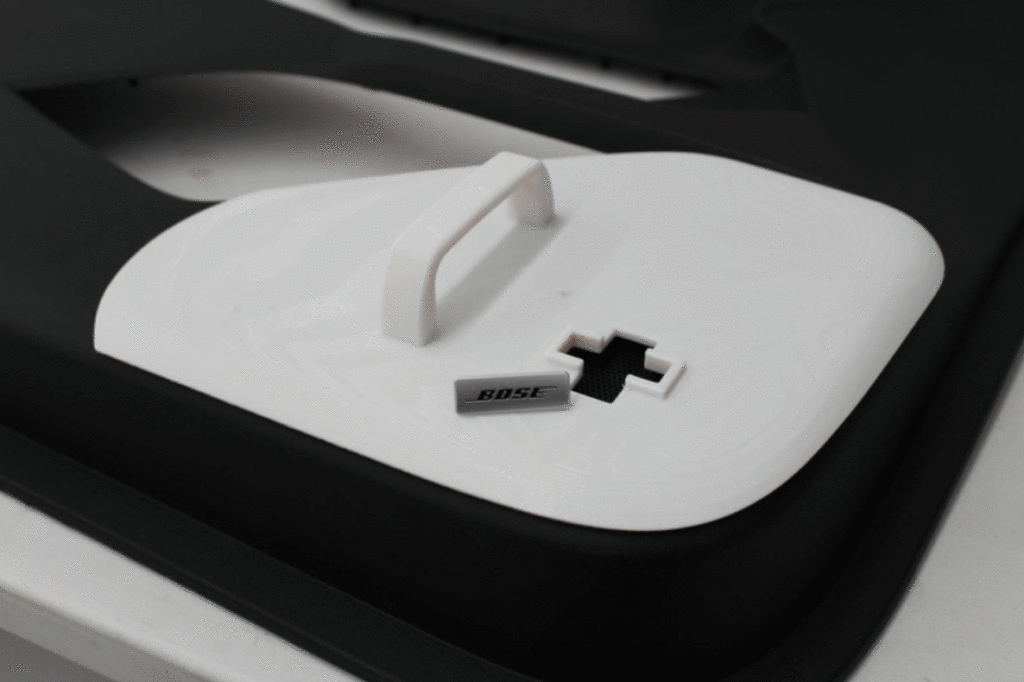
La herramienta de manufactura fue diseñada por nuestro equipo de Diseño para cubrir perfectamente la silueta de la bocina y marcar el lugar exacto donde el logotipo deba ser colocado.
El tiempo de fabricación fue de 9 horas y el costo de 200 USD. La pieza tiene un peso de tan sólo 300 gr.
Sin duda, una herramienta que logró generar grandes ahorros, estandarizar procesos y mejorar la eficiencia de la operación de la planta.