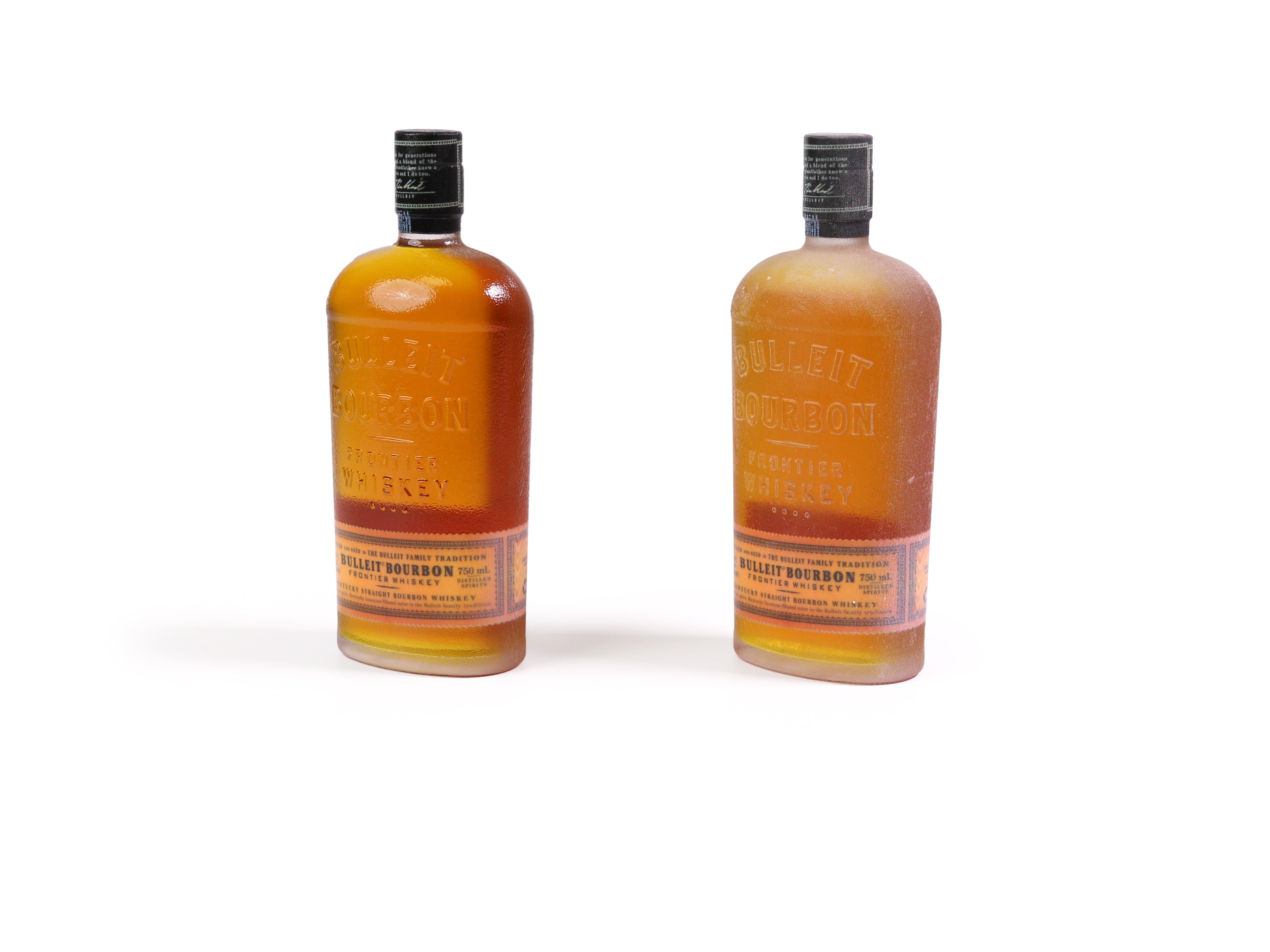
La Impresión 3D en la industria aeronáutica, ha sido donde mayor adopción se ha logrado. Hoy en día, el 68% de las empresas del rubro aeroespacial y defensa, utilizan la impresión 3D como una herramienta de sus procesos, o como la base de ellos.
Las aplicaciones van desde un prototipo, hasta la producción de partes que hoy en día, han vuelto las turbinas y motores mucho más eficientes.
Para fabricar estas herramientas, en ocasiones se recurre a maquinar en metal o acetales varios componentes de formas básicas para crear la herramienta. Dejando de lado la ergonomía, peso ligero y simpleza del diseño.
La Impresión 3D en Aeronáutica, rompe con ese concepto, ya que permite crear herramientas de manufactura completamente a la medida, que no solo ahorraran en peso, generando mayor ergonomía, si no que mantendrán una resistencia suprema y precisión dimensional.
Guías de taladro
OEM’s de aeronaves, utilizan guías para taladro y remachado de componentes fabricados en 3D. Así son 50% más ligeros y ergonómicos, sin descuidar la precisión.
Herramientas que permiten posicionar objetos para su correcto ensamble. Muchas empresas utiliza Fixtures impresos en 3D para asegurar el correcto ensamble de sus componentes.
Sistemas pokayoke
Por su flexibilidad y adaptabilidad, con impresión 3D es muy simple hacer guías pokayoke para ensamble o colocación de piezas, cuando estas mismas son complejas en forma.
Materiales metálicos como Titanio y Aluminio o termoplásticos básicos como ABS, PC y Nylon. Llegando hasta termoplásticos de alta resistencia térmica como PPSF, PEEK o Ultem o mecánica como el Nylon 12 Reforzado con Fibras de Carbono y Kevlar .
45 materiales en 7 tecnologías, y con un volumen de construcción de hasta 90x60x90 cm, hacen que tus proyectos lleguen a nuevas alturas.
Pruebas de funcionalidad
Algunas empresas de desarrollo de aeronaves a la medida, utilizan la impresión 3D aeronáutica para probar la funcionalidad de partes principales y así verificar diseños.
Mejoras de ergonomía
Con ayuda de la Manufactura Aditiva, varias empresas conceptualizan y prototipan los toolings que formarán parte de su proceso, en materiales plásticos para revisar ergonomía y funcionalidad, antes de fabricar en titanio.
Replicado a escala
Se ha utilizado la impresión 3D en aeronáutica para probar en túnel de viento la funcionalidad y comportamiento de algunas partes del avión. Incluso se han replicado aviones a escala para probarlos con sistemas de control remoto.
Hoy en día, los materiales compuestos son el siguiente paso de la aviación. Sin embargo, la elaboración de los moldes y pruebas toma mucho tiempo. Con Manufactura Aditiva para la industria aeroespacial, empresas alrededor del mundo, fabrican moldes para piezas de prueba, validación e incluso uso final.
Algunos materiales tienen la capacidad de soportar los tratamientos de curado y horneado de una pieza de fibra de
carbono. La ventaja, el molde puede ser más ligero, de menor costo y sobre todo de un delivery time mucho menor que los moldes tradicionales de aluminio o material compuesto.
Además, permite la creación de geometrías complejas, que de otra manera no podrían ser manufacturadas. Tal es el ejemplo de los moldes solubles.
Cores solubles
Algunos materiales de impresión 3D aeronáutica son solubles en químicos o agua, por lo que fabricar cores de formas complejas, permite construir piezas de material compuesto como tuberías y posteriormente, desaparecer el centro, permitiendo así, geometrías antes imposibles.
Moldes para vacio
Por su resistencia, los materiales de impresión 3D pueden servir para fabricar moldes que sólo requieren de vacío para formar la pieza de material compuesto. La ventaja, formas complejas en muy poco tiempo.
Alta temperatura
Para piezas de material compuesto que requieren de un proceso de horneado, es elemental contar con materiales de alta temperatura. Para ello, puedes utilizar Ultem 1010, el cual resiste hasta 230°C.
Uno de los retos más grandes de la industria aeroespacial es, ¿cómo disminuir costos de manufactura a tan bajos volúmenes?
En ocasiones, un pedido de piezas aeroespaciales no excede las 1,000 unidades, además de sus cambios constantes en la búsqueda de la reducción de peso. La Manufactura Aditiva permite romper esa barrera, produciendo piezas de uso final que puedan ser certificadas por organismos como la FAA y EASA para su función correspondiente en un avión.
Hoy, se estima que en los nuevos aviones fabricados por las grandes armadoras, el 5% de sus partes son piezas plásticas o metálicas comienzan a ser fabricadas con tecnologías de impresión 3D, principalmente en el sector de Interiores. Se espera una alza al 15% en los siguientes años.
Ductos ECS
Actualmente puedes fabricar ductos en materiales de alta resistencia a temperatura con la ventaja de tener libertad de geometrías, menor peso y reducir costo de inventarios por refacción o mantenimiento.
Fuel Nozzle
El caso más famoso de impresión 3D aeronáutica en metal, GE fabricó en 2018 su inyector de combustible 30,000. Un inyector reducido de 20 piezas a una sola, con 25% menos de peso y 5 veces más resistente.
Housings
Muchos componentes internos del avión que portan alguna tecnología indicativa, en ocasiones cambian debido a que la tecnología que portan, evoluciona, por lo que fabricar sus reemplazos con 3D es una opción mucho más viable que quedar obsoletos.
Obtén acceso a más de 300 impresoras 3D industriales, lo que representa tiempos de entrega cortos y precios accesibles, pero sobre todo, flexibilidad de fabricar tus proyectos en más de 45 materiales con tamaños de una sola pieza de hasta 90x60x90 cm en cualquier parte de México, sin salir de tu planta.
Contáctanos para llevar a tus instalaciones nuestro Workshop avalado por el Aerocluster de Querétaro, que ha generado grandes resultados en empresas como Safran, Albany, Brose, Adient y muchas más.