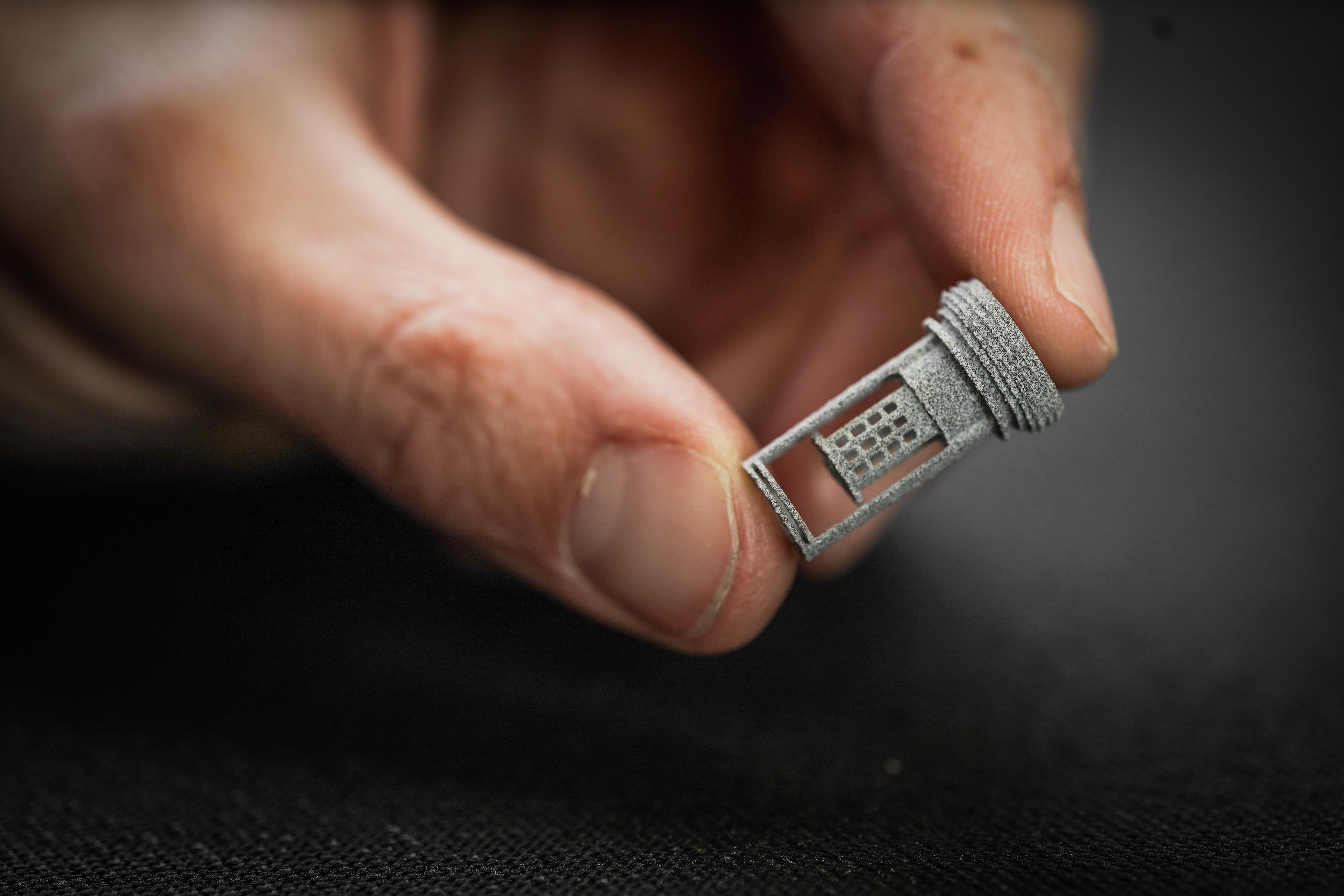
Bridge Manufacturing con Impresión 3D es una manera de llegar más rápido a tus clientes y usuarios, sin la necesidad de moldes o altas inversiones.
Todo producto que es lanzado al mercado o producido en masa, pasa por un proceso largo de diseño, validación y producción. En ocasiones, el producto ya debe de estar en el mercado, pero los retrasos en este proceso pueden afectar de gran manera al propio proyecto.
Para ello, se utiliza Bridge Manufacturing, la cual consiste en poder fabricar y lanzar al mercado el producto en paralelo se desarrollan los moldes y herramientas de producción necesarios. Acelerando el tiempo al mercado.
Una vez que ha sido validado el diseño y aprobado para producción, se comienzan a fabricar los moldes de inyección de plástico. Estos moldes normalmente son fabricados en aceros y toman de 6 a 8 semanas (en un caso simple), en otras ocasiones toma meses.
Durante ese tiempo, el producto no puede ser introducido al mercado y hay que esperar a que el molde esté listo. Cuando el molde se encuentra listo, se deben de hacer pruebas, ajustes y configuraciones al mismo, que en ocasiones, añaden 4 a 6 semanas más al desarrollo.
Ya liberado el molde, se instala en las máquinas de inyección y se comienza con la producción y posteriormente, la salida al mercado.
Pero en ese tiempo, ninguna pieza pudo ser utilizada, vendida o introducida al mercado.
Para cerrar esta brecha, se utiliza la manufactura puente. Este tipo de manufactura tiene varias opciones de realizarse, ya sea con soft tools de aluminio para producciones de decenas de miles, o bien, mediante la impresión 3D, también para decenas de miles en algunos proyectos.
Dependiendo el presupuesto y alcance del proyecto se utiliza una o la otra. En ocasiones, ambas, dependiendo de lo crítico del proyecto.
Para la fabricación de soft tools, se utilizan moldes de aluminio simples, que toman en fabricarse alrededor de 15 días. Estos moldes son manuales o semi automáticos, y no tendrán todas las funcionalidades y/o características del molde final.
Servirán para fabricar las piezas en el mismo material para el que fue diseñada la pieza. Este molde, normalmente se coloca en un porta moldes previamente fabricado, lo cual permite disminuir sus costos y tiempos de fabricación. El molde tendrá un tiempo de vida limitado, pero que puede funcionar mientras el molde final está listo.
Al usar la manufactura aditiva, puedes pasar directamente del diseño a la fabricación de piezas sin tener que invertir en un molde, utilizando diversas tecnologías como FDM. La tecnología a elegir dependerá del presupuesto y alcance del proyecto.
La principal ventaja de usar cualquiera de estas tecnologías de impresión 3D, es que no hay que esperar días a obtener las piezas. En cuestión de horas puedes estar obteniendo cientos de piezas, listas para ser introducidas al mercado.
En cuestión de costos, el valor unitario puede sonar alto, pero recuerda, no estás pagando por moldes o costos de setup, por lo que se generan grandes ahorros ante un número de piezas.
Adicionalmente, esta manera de hacer manufactura puente, ayuda a tener en el mercado productos de respuesta rápida, en lo que se fabrican los moldes para la masificación de las piezas, como el siguiente ejemplo ante el caso COVID-19.
Ante la situación del COVID-19, muchas piezas han sido escasas para afrontar la demanda global y nacional. Tal es el caso de las caretas de protección tipo escudo.
Al estar agotadas en el mercado, diversos proveedores comienzan a expandir su capacidad de manufactura, pero para ello, requerirán de más moldes, lo cual ya revisamos previamente el tiempo y proceso. Una vez que se tiene un diseño 3D nuevo, se comienza con la producción del molde.
De ejemplo, el desarrollo de un molde de aluminio para producir la parte plástica rígida de 50,000 caretas, tiene un costo de aproximadamente $4,000.00 usd y tomará de entre 4 y 6 semanas en estar listo. Ese molde comenzó a fabricarse a finales de marzo, pero estará listo para mediados/finales de abril. Se revisó un molde de mayor capacidad y rondaría los $20,000.00 USD para una manufactura de cientos de miles, pero demoraría más de 3 meses en estar listo.
Mientras, la única manera de tener caretas en los hospitales y con personal médico, es mediante las tecnologías de impresión 3D y fabricación digital. Con el diseño listo, en cuestión de un par de horas ya se tenían las primeras piezas, las cuales permitieron verificar diseño y validar.
El diseño se optimizó y se logró reducir el tiempo de manufactura drásticamente. Con una sola impresora de FDM, se pueden producir hasta 60 máscaras por día. En equipos como MJF o SLS hasta 90 y estamos mejorando el diseño para que sean muchas más. Con ayuda de cientos de impresoras 3D conectadas en la Iniciativa de Aditiva por México, la capacidad diaria de producción se extiende a miles de piezas diarias.
Una vez terminada la impresión, se empaca cada pieza y es entregada de inmediato a los hospitales y centros de salud donde más se necesita.
Este caso puntual, habla de los beneficios de hacer una manufactura express y cubrir el gap entre el diseño y el día en que las piezas están listas.
Pero en otras ocasiones, el volumen de producción de piezas total del proyecto, no justifica inversiones en moldes, por lo que el producto se olvida, o se prefiere no lanzar al mercado.
Otras ocasiones, como diversos de nuestros clientes, cambian y actualizan sus diseños cada año, lo que les permite ser más flexibles a las demandas del mercado y lo que sus clientes piden. De esta manera, la obsolescencia nunca llegará a sus productos.
La impresión 3D puede ser una solución para transformar modelos de negocio donde pocas piezas, puedan ser producidas y así cerrar la brecha entre una idea y su potencial adopción en el mercado.